Additive Processes
Spray Coating
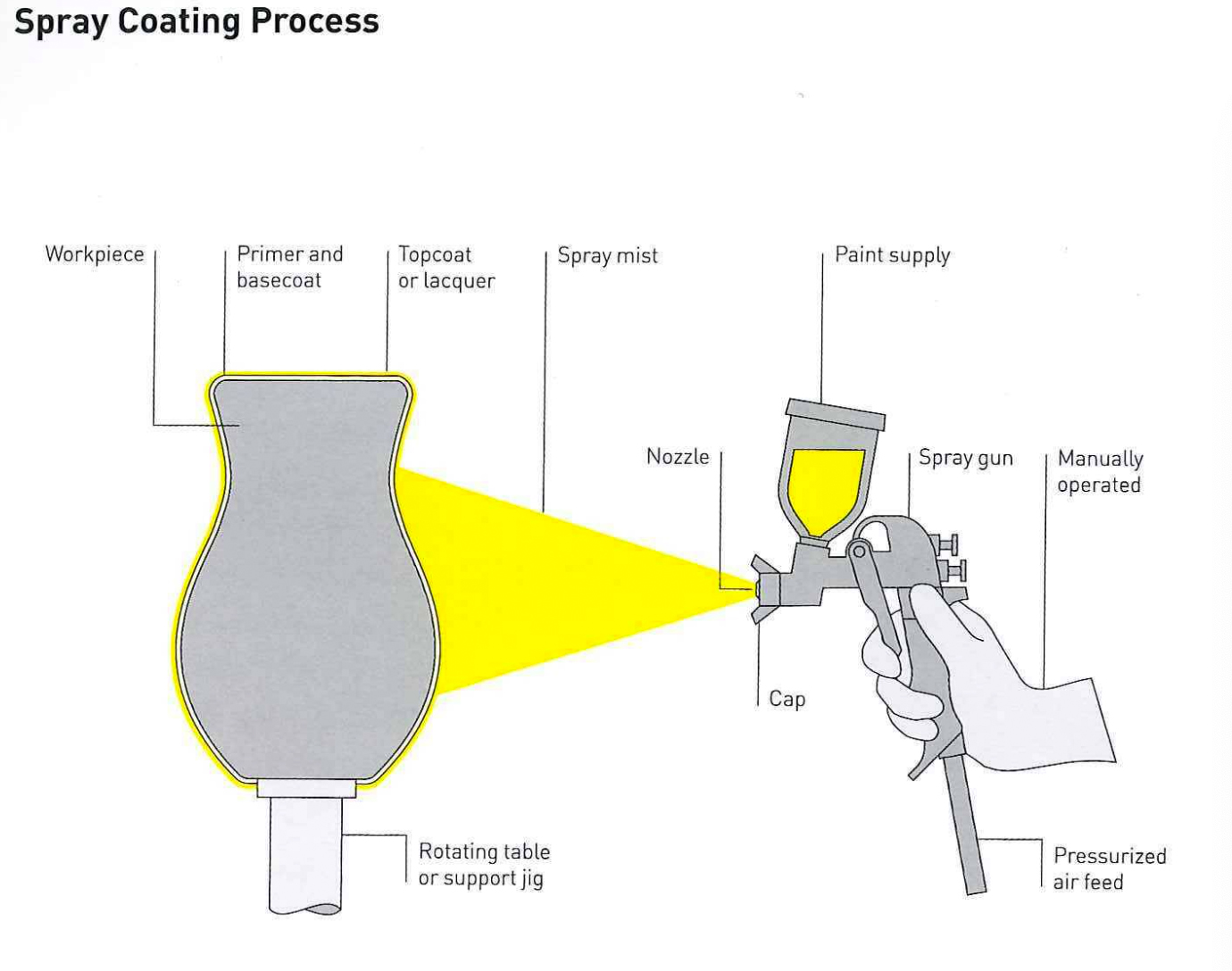
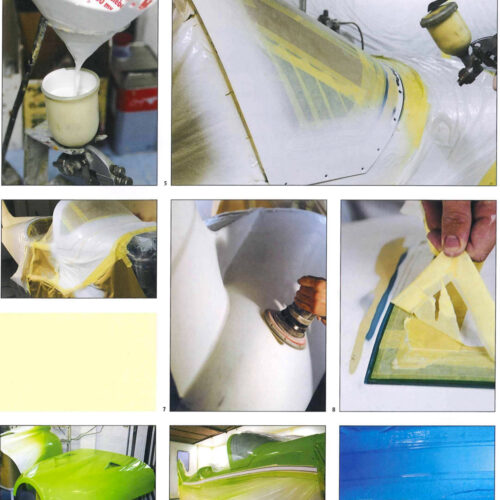
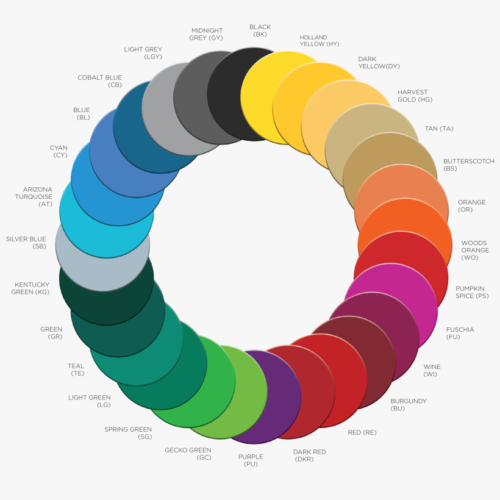
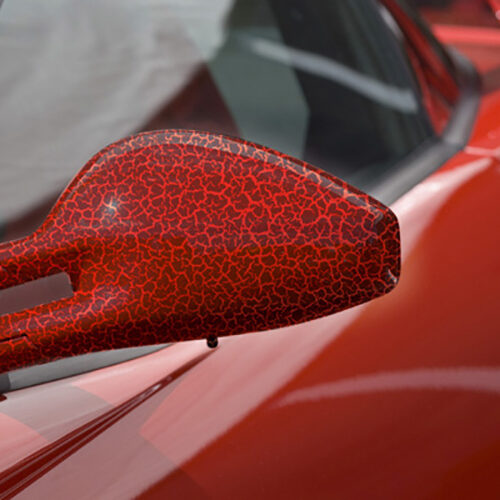
Powder Coating
This dry finishing process is used to coat a range of metalwork by either electrostatic spray or a fluidized bed. The powder adheres to the workpiece electrostatically and is cured in an oven to produce a glossy protective coating. Read more.
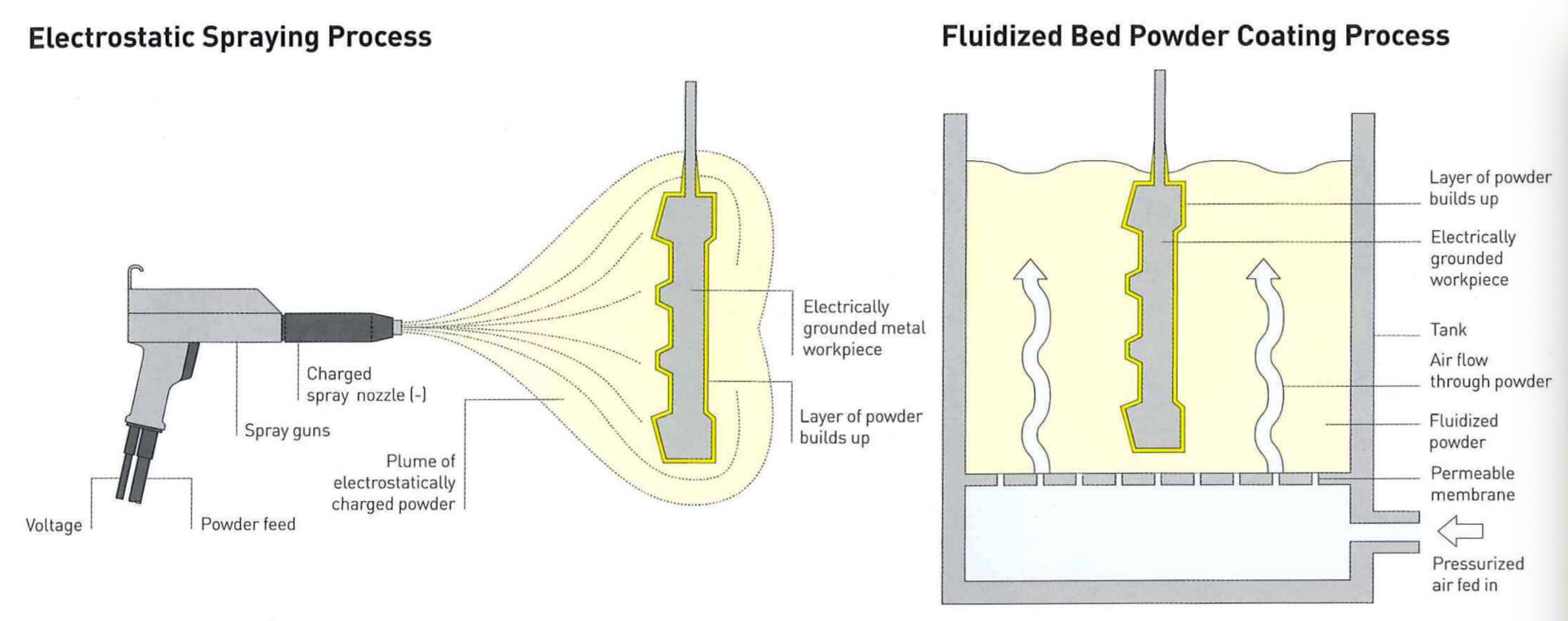
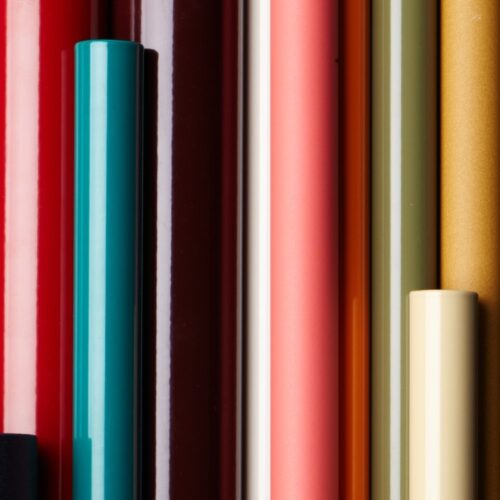
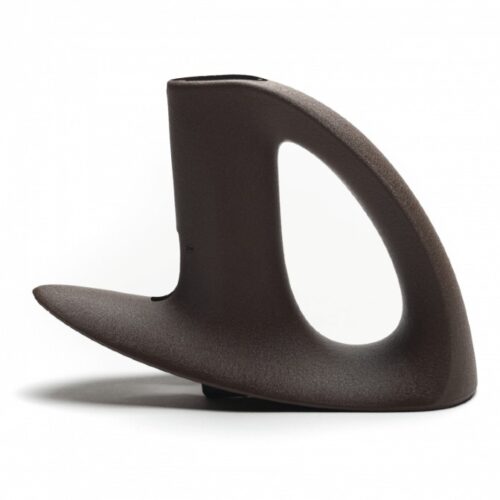
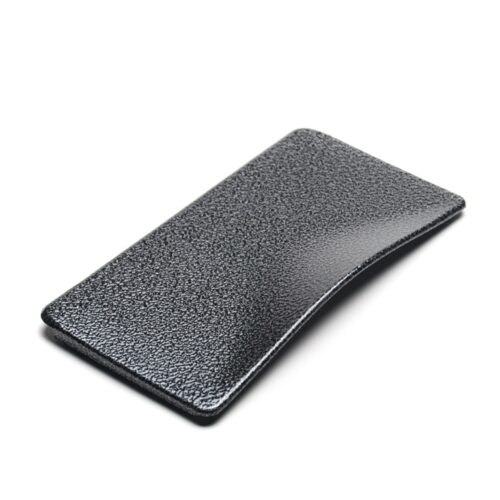
Anodizing
Anodizing refers to a group of processes that are used to treat the surface of metals(aluminum, magnesium, and titanium.). The workpiece is made of the anode and submerged in an electrolytic solution. The process builds up the naturally occurring oxide layer on the surface of the metal. The film is hard, protective, and self-healing; aluminum oxide is inert and among the hardest materials known to man.
Anodizing has many benefits Including hardness, ease of maintenance, color stability, durability, heat resistance and corrosion resistance, and it is non-toxic。
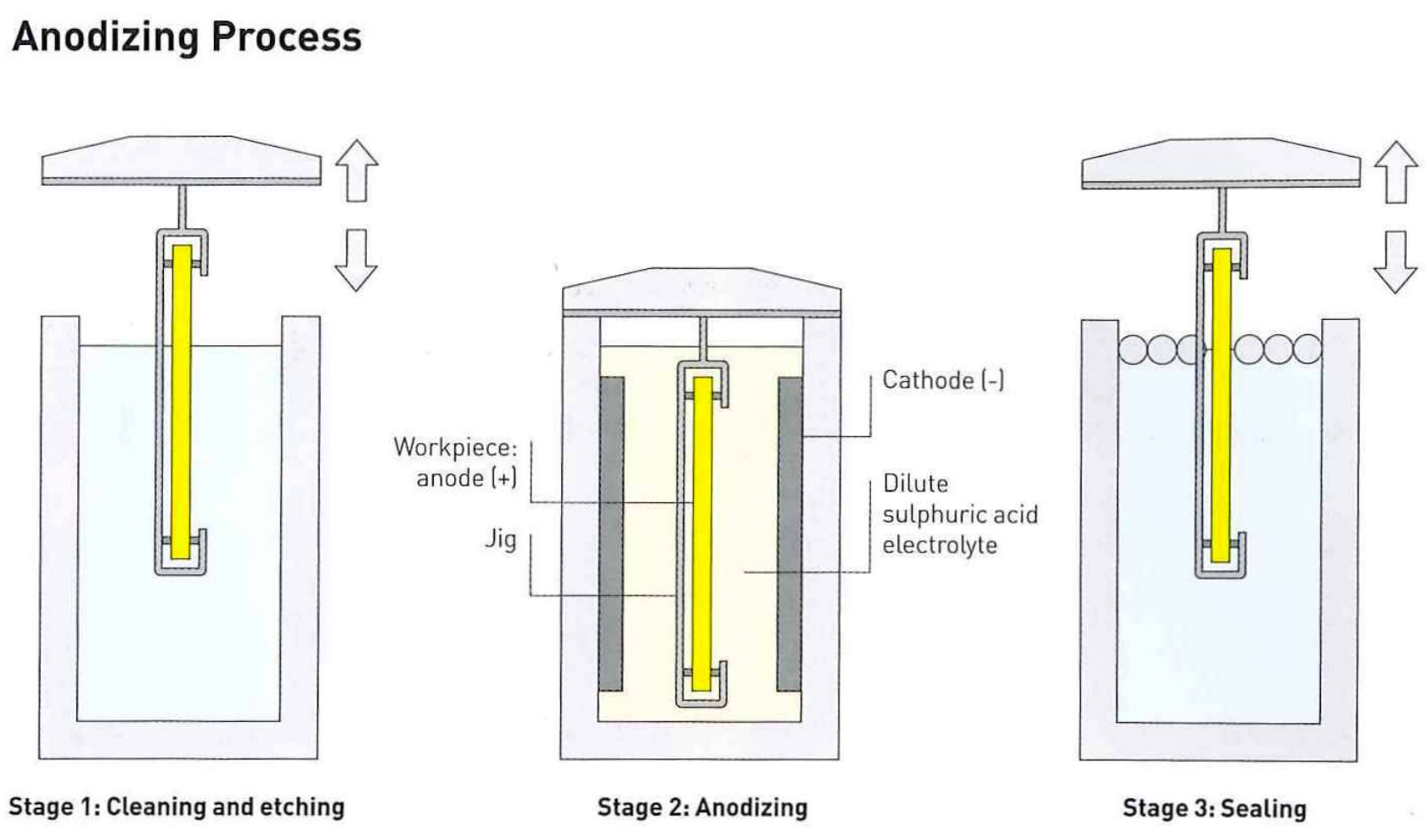
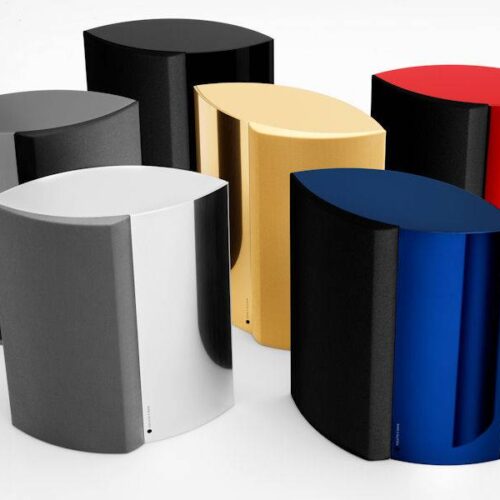

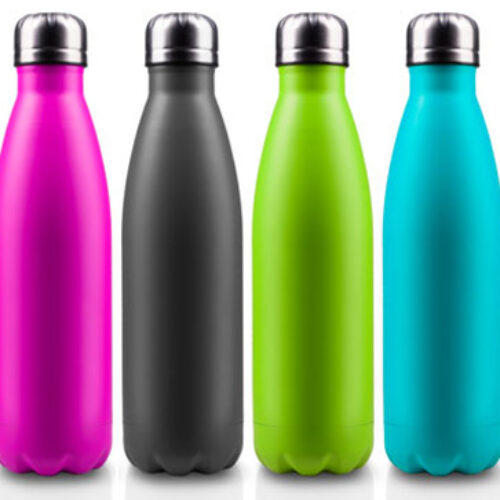
Electroplating
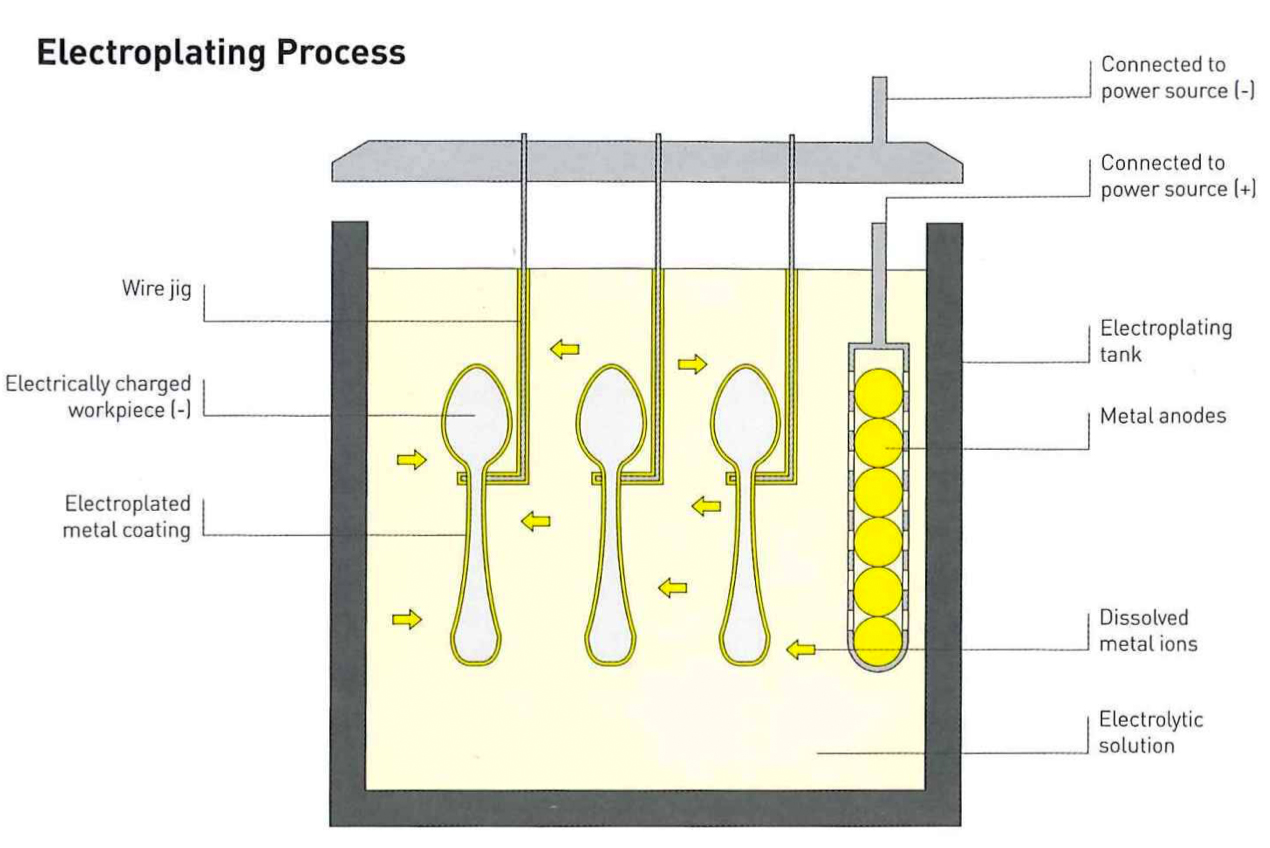
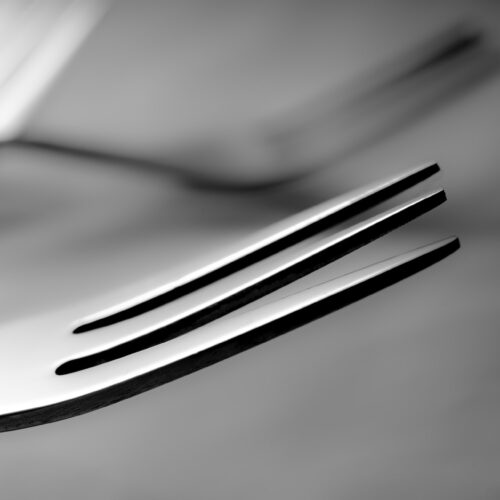
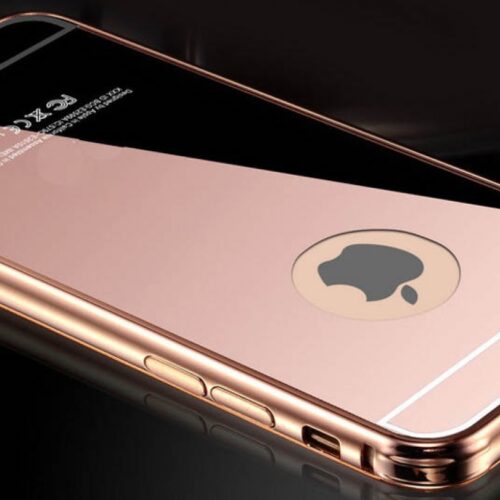
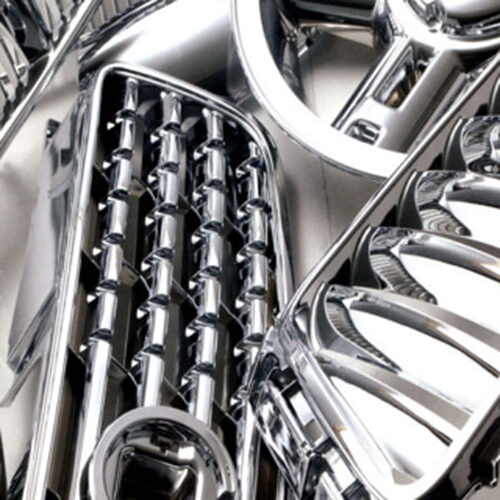
Galvanizing
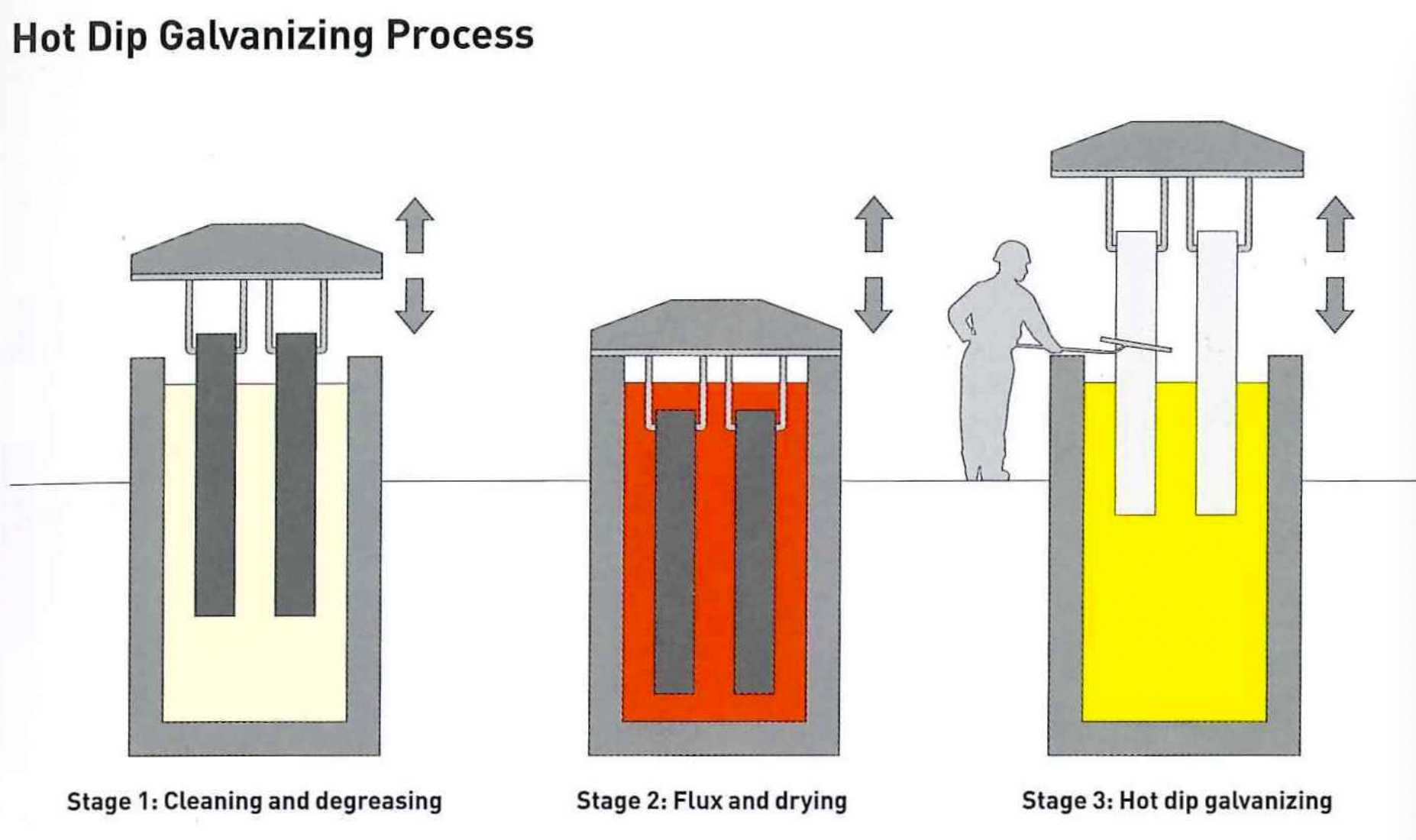
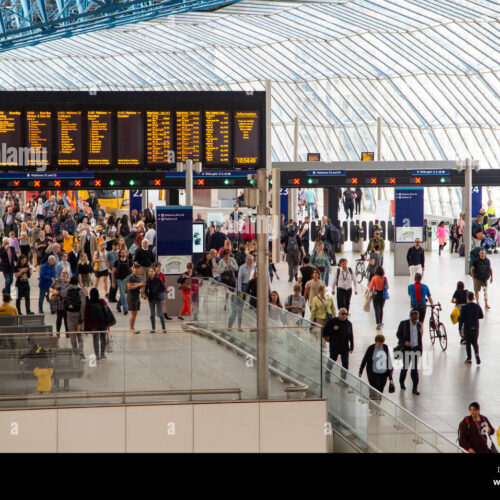
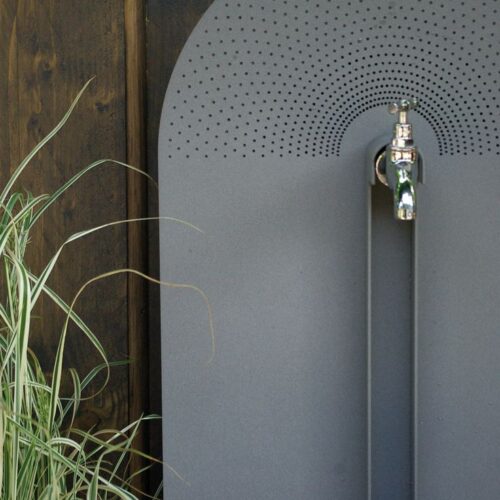
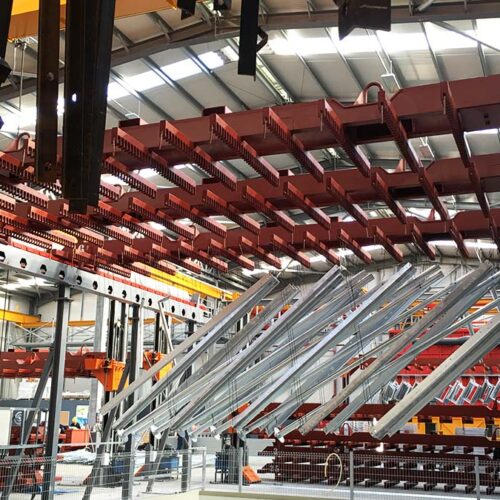
Vacuum Metalizing
Vacuum Metalizing also known as physical vapor deposition (PVD) and sputtering, vacuum metalizing process is used to coat a wide range
of materials in metal to create the look and feel of anodized aluminum, chrome, gold, silver, and other metals.
This process combines a very high vacuum and an electrical discharge that vaporizes almost pure metal (most commonly aluminum) in a vacuum deposition chamber. The plume of vaporized metal condenses onto surfaces, coating them with a high-gloss film of metal.
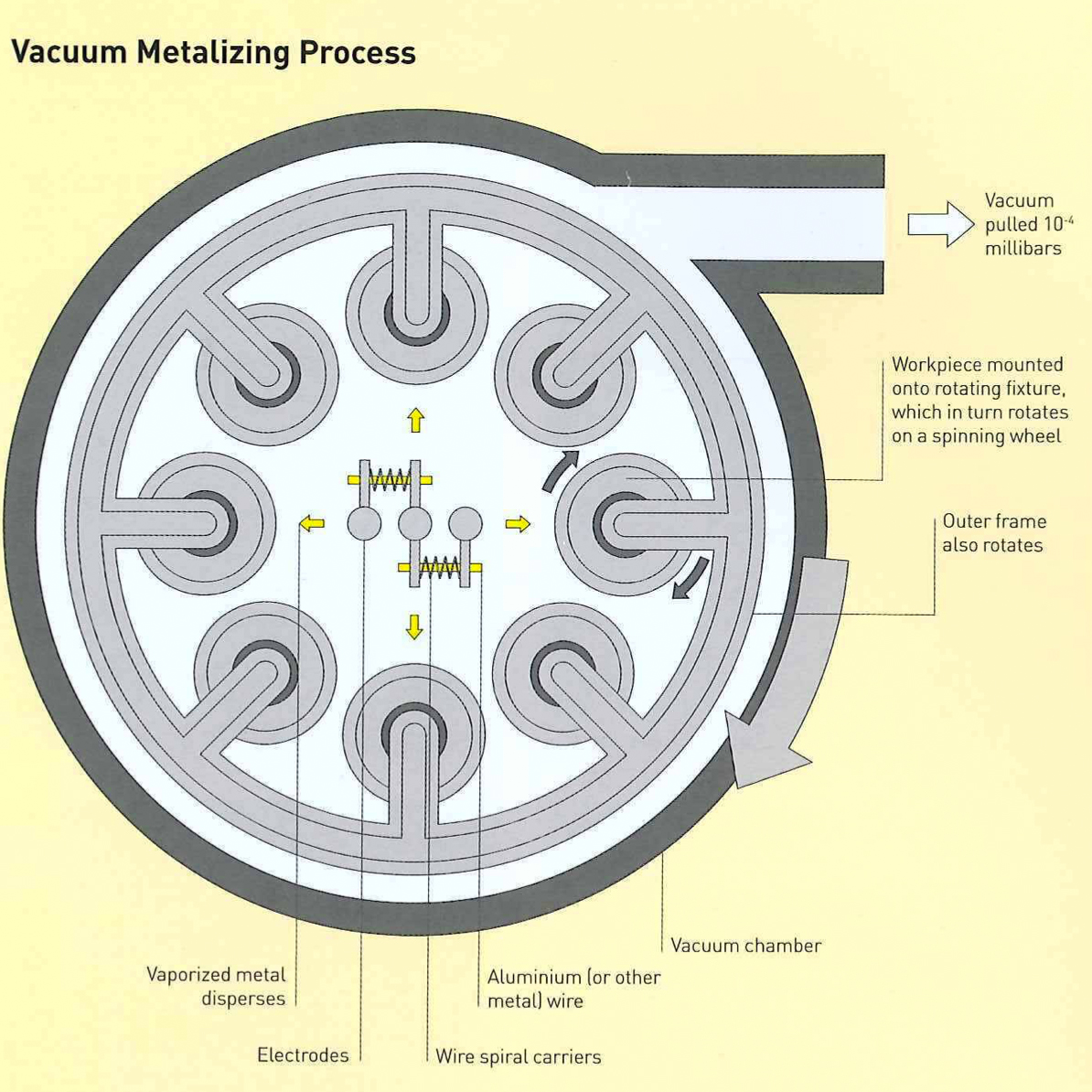